- Researchers from RMIT University have created an incredibly strong lattice structure.
- The structure is 3D printed from titanium alloy and is 50 percent stronger than materials as dense currently used in aerospace applications.
- While manufacturing the structure could be tricky, it’s applications extend to medical devices, bone implants and even use in aircraft.
As we gravitate toward reusing rockets. we may have to reconsider the materials that are used to build these rockets. For the most part aluminum and titanium alloys are used in rockets and these metals can be costly.
So it’s a good idea for humanity to develop something stronger that would stand up to the constant abuse during rocket launches and potentially in other applications. Enter researchers at the Royal Melbourne Institute of Technology (RMIT) University who reckon they have developed the strongest material for aerospace applications yet. The findings were published in the research article Titanium Multi-Topology Metamaterials with Exceptional Strength. That article is open access so you’ll be able to read in-depth about the testing the team did to arrive at their conclusion.
Dubbed Unobtanium, no we’re just joshing you. The material in question is a new lattice structure made possible through 3D printing.
“We designed a hollow tubular lattice structure that has a thin band running inside it. These two elements together show strength and lightness never before seen together in nature,” RMIT’s Distinguished Professor Ma Qian said in a statement.
“By effectively merging two complementary lattice structures to evenly distribute stress, we avoid the weak points where stress normally concentrates,” Qian added.
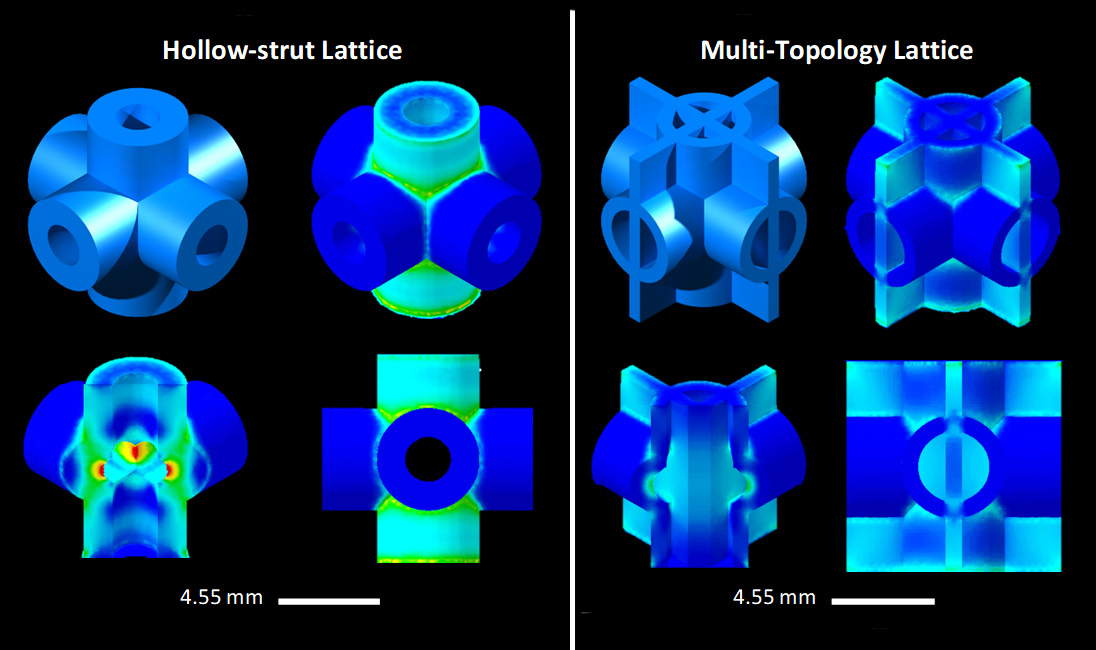
The solution is elegant in its simplicity and robust in its strength. According to the researchers, this titanium lattice structure is 50 percent stronger than cast magnesium alloy, an alloy of a similar density used in aerospace applications. Stress placed on the structure was half that in a similar lattice as illustrated above.
The lattice can be millimetres or several metres in length making it suitable not only for use in rockets but in bone implants, medical devices and aircraft parts as well. The lattice can withstand temperatures as high as 350°C but with tweaking, the researchers believe it could withstand temperatures as high as 600°C.
“Compared with the strongest available cast magnesium alloy currently used in commercial applications requiring high strength and light weight, our titanium metamaterial with a comparable density was shown to be much stronger or less susceptible to permanent shape change under compressive loading, not to mention more feasible to manufacture,” RMIT PhD candidate and lead author on the study for this lattice, Jordan Noronha said.
The one problem here is in the manufacturing of this lattice. The structure is 3D printed using laser powder bed fusion. This process sees metal powder melted into place by a high-powered laser beam. Like us, you probably don’t have such a machine at home and the researchers note that access to such a machine may make creating this lattice tough.
“However, as the technology develops, it will become more accessible and the printing process will become much faster, enabling a larger audience to implement our high-strength multi-topology metamaterials in their components. Importantly, metal 3D printing allows easy net shape fabrication for real applications,” Noronha explains.
We hope that this lattice makes it to the mainstream, well, the mainstream of additive manufacturing in the aerospace and medical fields at least.